
Drive-o-copter
Just like the name implies, the Drivocopter is a machine that can both drive and fly. Creating a bottom assembly with wheels and an upper quadcopter causes multiple design, weight, and power issues. A prototype was assembled prior to my arrival (primarily by Caltech student Terry Suh ‘19), but I assisted with modifications and improvements to the electronic box, spring holders, and wheel casters and achieved weight reductions.
(Note: portfolio cover image from Luis P)
Electronic Box
Old Version
The old box was well designed, but it only carries the electronics for the bottom portion of the drive-o-copter. Once the design team realized that the upper flying portion of the drive-o-copter could not be separated into a self-sufficient module, the decision was made to move the electronic components to the flying part and the battery to the driving part of the vehicle. The decision was made to place two more circuit boards into the electronic box.
New Version
This newly designed electronic box organized all of the drive-o-copter’s electronics; hence, the location for each board was predetermined and holes were made accordingly. The box followed the outline of the carbon fiber plate (shown above) so that the available space was maximized in that limited area. The updated model was shorter in length and height for lighter weight (50%) and aesthetics. The position of the boards was rearranged so that the board that needs the most vertical space is now in the middle, and it is also well ventilated as some boards can get hot fairly quickly.
Spring Holder
CAD
Changing the type of spring and the spring’s attachment to the wheel apparatus also improved the overall function and design. A centrally located torsion spring, rather than one on both ends, provided a simpler solution to attach the wheels to the main body as well as a better shock absorption which was proven by testing. The screw holes connecting the two parts needed to be countersunk to fit 20mm M2 screws, and space on the opposite side had to accommodate tightly-fitted M2 nuts.
Built Product
Undergraduate student, Camila Buitrago (‘22), designed the tube insert for the spring to connect to the carbon-fiber rods (which is connected to the wheels), but I helped finish the actual building of the new spring system. All of the parts had to be hammered into each other. Ultimately, the one-spring system was a more efficient design that cut space and weight.
Wheel Caster
Weight Reduction
The previous design can be seen in the image above in the spring holder section.
Improvements to the wheel casters resulted in significant weight reduction. By eliminating the front and back portion of the casters, functions were maintained but the wheel apparatus weight was reduced from 36.59g to 16.99g.
The Drive-o-copter project remains ongoing and will be incorporated into Caltech’s Engineering (ME/EE/CS 75) course, in hopes that progress will enable the machine to participate in the next circuit of the DARPA SubT Challenge in February 2020.

Printed New Electronic Box w/ Support
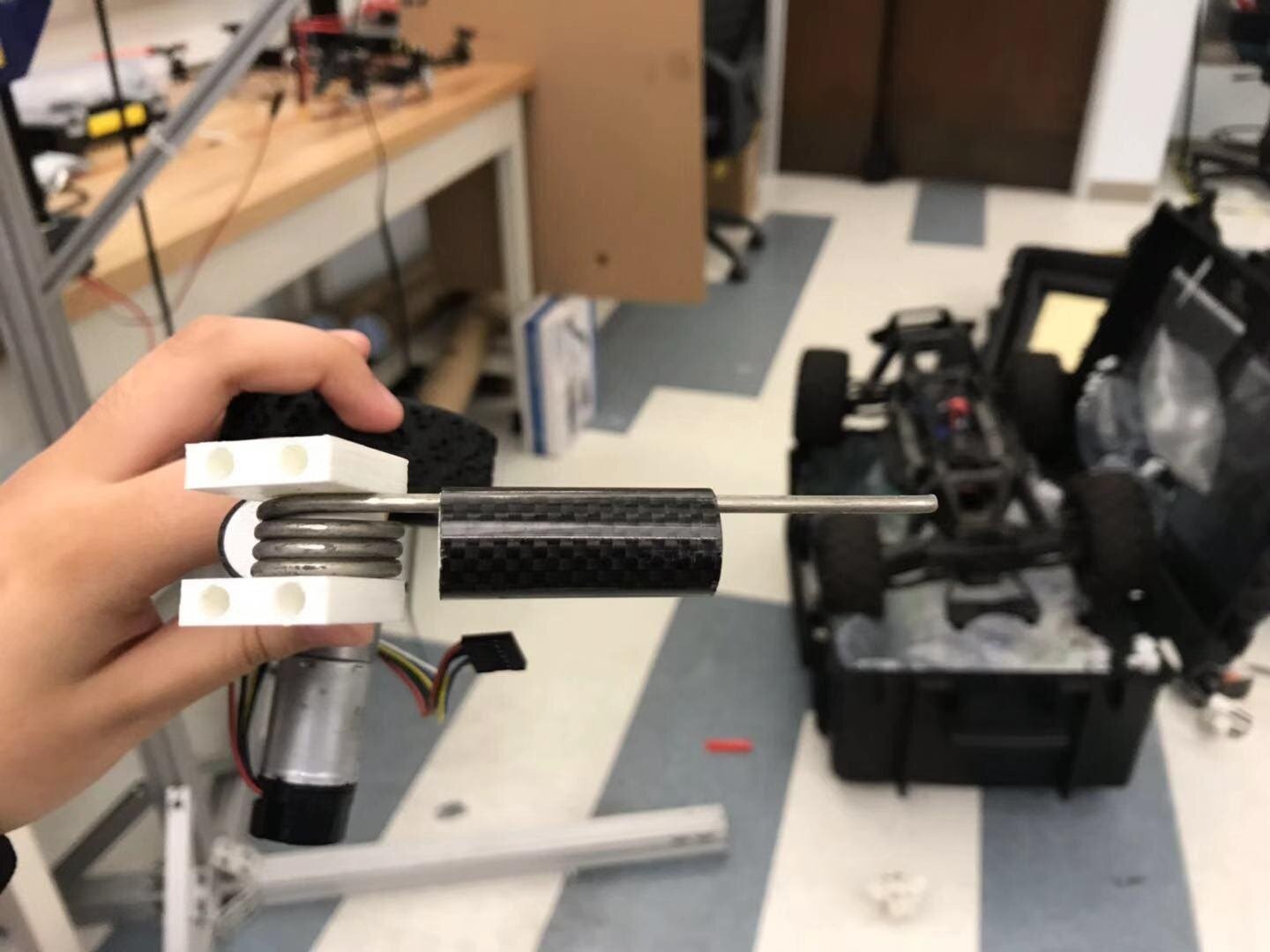
Torsion Spring

What to hammer?

New Box w/ New Plate

New Wheel Caster Printed